Visible Mending
At Production Mode, we LOVE clothes- not just our collection, but very the idea of clothes and what they represent: how certain pieces are so wrapped up with our identities and evoke memories of events, people, places, and even eras. Our designer, Jamie Hayes, even created two bodies of artwork devoted to this idea.
To us, clothes are precious. In addition to the joy they bring us, we value the vast amount of natural and human resources necessary to create clothing. The fusion of these ideas is the foundation of our commitment to slow fashion.
In that spirit, we introduce our Visible Mending program, led by designer and mending expert Lucy Leith. By darning holes, patching tears, & reinforcing seams, we can repair your garments, while adding another layer of interest and history to your clothing. We invite you to be part of this collaborative process.
Darning
Using thread to weave a fresh new patch of threads over a hole or tear, this process can be traced back to the early 18th century.
Invisible Mending
Using different mending techniques and matching threads that blend in with the fabric of the garment. Look close, or you’ll miss it!
Embroidery
A whimsical way to cover up holes. A great option for moth-eaten garments.
Running Stitch Patchwork
A technique that uses short running stitches and scraps of fabric to reinforce a tear or hole—inspired by the Japanese form of visible mending called Sashiko. Sashiko originates in the Edo Period in northern Japan around the 17th century and was developed to extend the life of valuable fabrics in a decorative way. This technique can be used to draw attention to the raw edges that are left behind by each tear and create a beautiful point of interest. Small patches of scrap fabrics are incorporated, using layers of these stitches to bond the layers together.
Machine Darning
Creating a strong, durable fabric by stitching the fabric to a backing many times over. Since this much stitching makes the fabric quite stiff, we reserve this technique for items like denim jeans. A good option for crotch repairs, especially if you want the mend to blend in.
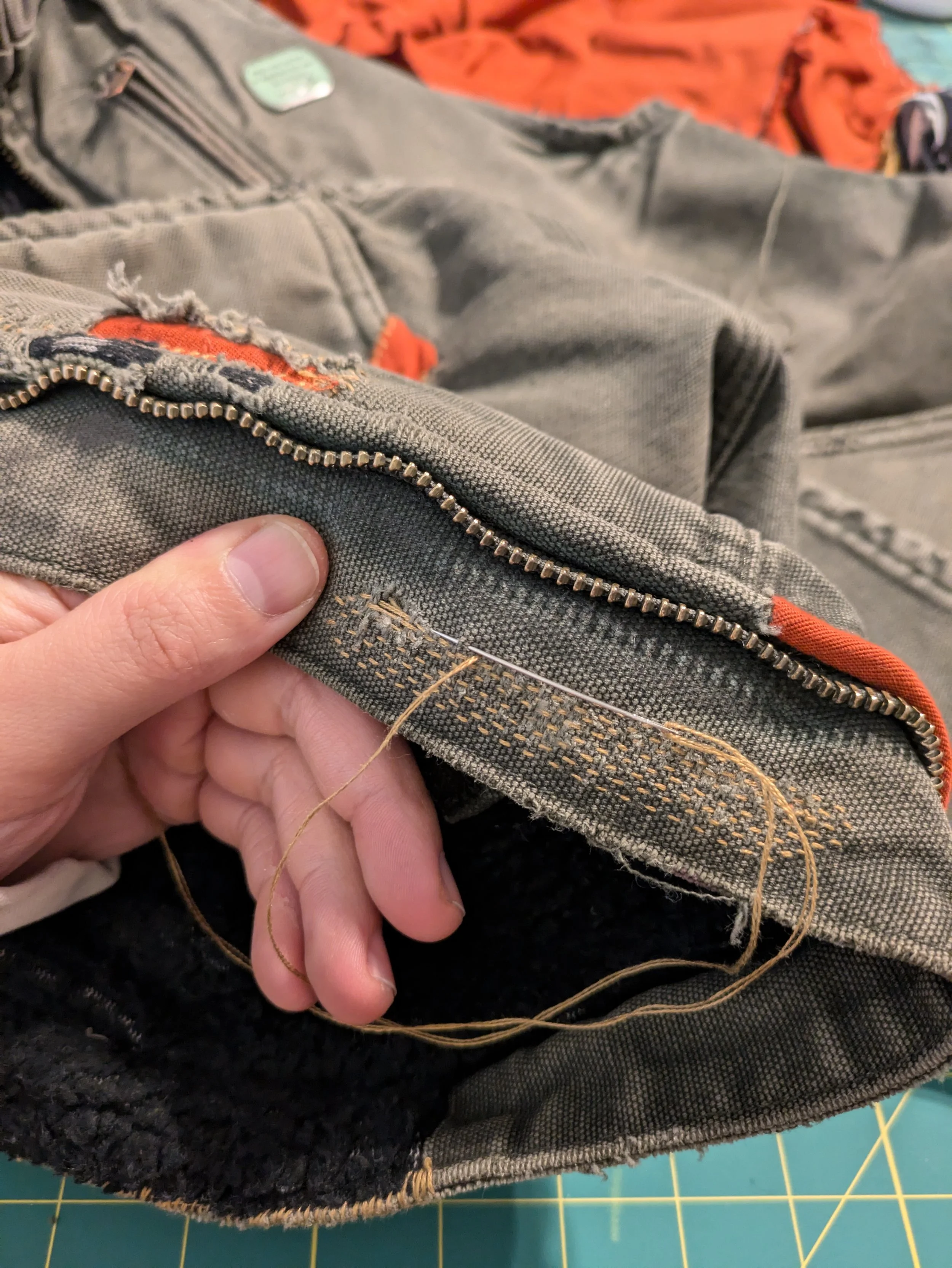
Take a peek at the process
The mending process begins with choosing colors and mending techniques; in this case, darning with earthy green yarns.
Darning starts with parallel lines of yarn or thread that weave through the surrounding fabric to evenly fill the space where the hole used to be.
Horizontal yarns weave in and out to create a solid fabric.
The completed sweater.
This lightweight shirt was worn all the way through at the elbow.
We used a similarly lightweight fabric to patch up the hole. Here is the sleeve inside out, where the patch will be hidden on the inside of the sleeve.
Simple running stitches hold the patch to the sleeve. On the outside, these yellow lines will blend in with the yellow lines of the plaid.
This client gave us full creative control, so we decided to showcase the mend by continuing but warping the plaid lines.
The final mend. We left the worn out threads of the garment loose at the client's request.
This crotch repair began with basting (loosely stitching) and pinning a backing fabric to the inside of the pants.
This client wanted the mend to stand out, so we mimicked the unique zigzag stitching details of the pants by first drawing our design in chalk.
Machine stitching over the chalk lines.
A view of the inside of the pants post-mend.
The final design honors the geometric stitching of the original pant design.
The final view of the back of the pants.
Get in touch.
A consultation is offered free of charge by filling out the Visible Mending Intake form.
Pricing varies by the severity of damage to a garment, fabric, repair type, and shipping charges if applicable (we accept drop-offs as well).
Please allow 1-2 weeks for the garment to be in our care.